Building a Loading Dock
Designing a loading area requires some careful planning. A poorly designed loading dock increases the risk of accidents, like tripping or collisions between forklifts and pedestrians. It can also lead to traffic congestion and damage to goods and equipment. When it comes to planning the design, there are several factors to keep in mind:
Number of Bays
How many trucks will you need to accommodate? The average loading bay dimensions feature a door width between 7.5 and 10 feet wide, depending on the size of the trailer, along with a minimum of 12 feet between each dock. Consider these numbers when determining the number of bays your current structure can feasibly fit.
Type of Dock
It’s also important to know the type/design of dock you will build. There are a few different styles of loading bays:
Open or Open Platform
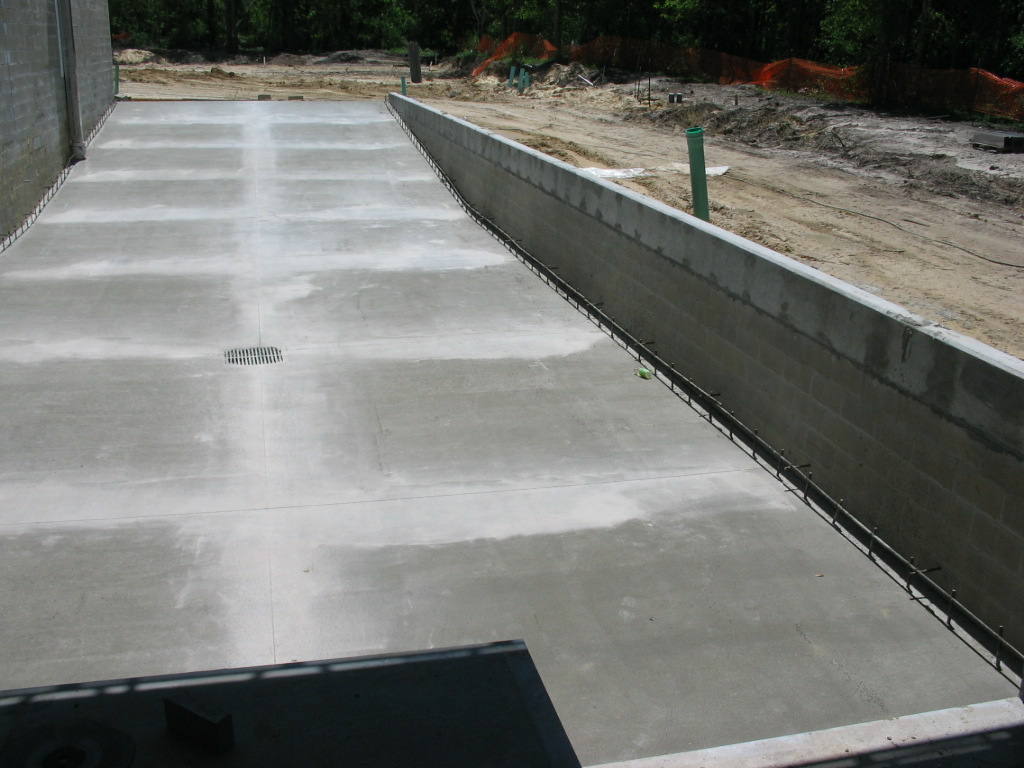
Publix Loading Dock by Elcamino502 is licensed under the Creative Commons Attribution-Share Alike 3.0 license.
This type extends from the building without any walls enclosing them, providing easy access and maneuverability. They don’t offer any protection against the elements, so they should only be used in mild climates.
Flush
This is the most common style, where the dock face is aligned flush with the exterior wall of the building. Trucks back up directly to the building, where dock levelers bridge the gap between the dock and the truck bed. This design helps minimize gaps while protecting goods from the weather.
Saw-Tooth
This style is named for its angular design, resembling the teeth of a saw. They are typically angled relative to the building, making it easier for trucks to maneuver and dock. A saw-tooth design is particularly useful in areas where space is limited or where direct access to the building is obstructed.
Enclosed
As the name suggests, this dock style is completely enclosed by the building, providing maximum protection against the elements. In this design, trucks enter through an overhead door to load and unload goods. This style is primarily used for businesses frequently handling sensitive or high-value products and is often the most expensive option because they require more materials, climate control, and security features.
Apron Area
Because trucks are so long, drivers need sufficient room to position the vehicle in front of the bay. The designated space to do this is called the “apron.” When designing the apron area of the dock, you’ll need to think carefully about the average length of the trucks. Maneuverability distance should be a good 5 to 10 feet, more than twice the size of the trailer.
Approach Angle
Whether trucks are traveling downward, upward, or on level ground to get to your loading dock may have a huge impact in how you design your bays. Proper bumpers need to be installed to factor in this angle so that trucks can park easily without causing damage to your building.
Safety Features
Every loading dock needs safety features, like dock levelers, bumpers, and safety barriers to prevent accidents. When designing your dock, consider the following:
- Dock levelers for bridging any gaps between the dock and the truck.
- Rubber or composite dock bumpers to prevent damage to your building (as mentioned in the section above).
- Guardrails or barriers around the dock to prevent falls off the edge, particularly in open platform designs.
- Emergency stop buttons and safety interlocks to prevent machinery from operating when unsafe conditions are detected.
- Audible alarms or visual indicators to signal when a dock is in operation or when a door is about to move.
- Overhead protection, like canopies or awnings to provide extra weather protection.
Maintenance & Upkeep
Loading docks aren’t that difficult to maintain, but you should still think about how much time (or money) you’re willing to put into upkeep.
Open docks generally require less maintenance, especially compared to enclosed docks, because they have fewer structural elements. However, they may need more frequent cleaning and weatherproofing.
Flush docks are close to the building, so maintaining the building’s exterior where the dock meets the structure is important. With this style, you’d have to regularly check dock levelers and bumpers.
In saw-tooth designs, the alignment and condition of the dock angles need regular checks to ensure they’re not causing undue strain on vehicles or equipment.
Lastly, enclosed docks tend to require the most maintenance because they are fully integrated into the building. They still require routine inspections, like all dock styles, but the internal environment also needs to be managed for temperature and humidity.
Elements That Can Increase the Overall Cost
As mentioned, enclosed docks are typically more expensive to build, so keep that in mind if you’re going with that style. Other options that could potentially increase the cost of your project include:
- The type of dock leveler you purchase. Hydraulic levelers are more expensive than mechanical or pneumatic ones, but they are easier to operate and are often more durable.
- Opting for a vehicle restraint system over basic mechanical wheel chocks.
- Sealing your dock to provide better weather resistance.
- The choice of material you use on the dock, dock bumpers, etc.
- Incorporating automated dock equipment, like dock doors and levelers.
- Installing and maintaining climate control systems.
- Implementing safety features like lighting, barriers, and alarms.
- Configuring special dock heights or angles for non-standard trucks.
Get Help Designing Your Loading Dock
There’s no way around it—a loading dock is a significant investment for you, so it’s crucial that you make sure you’re getting what you need and that it’s designed and installed correctly.
G&G Concrete & Construction can help you manage this type of project. We’ve been handling all types of commercial concrete projects in southeast Michigan for over two decades. Please contact us today to request a site assessment and project estimate.